Glue Wire Insertion
Overview
The design and supply of a bespoke machine were required to assemble polyamide strips and glue wire, forming a thermal barrier for use in aluminium double-glazed door assemblies. The polyamide strips are presented in 6500mm lengths, while the glue wire comes in roll form, but the exact lengths were not initially known.
The motivation for this project was partly driven by the Covid-19 pandemic. As a result of the pandemic, the client’s existing suppliers of thermal barriers (polyamide strips with pre-inserted glue wire) were unable to meet demand. To ensure business continuity, the client sourced alternative global suppliers for both the polyamide and glue wire as separate items. This created the need for an automated method to insert the glue wire.
The Challenge
As stated above, the polyamide strip length was specified as 6500mm; however, no length tolerance could be confirmed, meaning the machine needed to accommodate variations in length.
The alignment of the glue wire and polyamide strip had to be consistently repeatable without requiring operator intervention.
The Solution
The insertion machine consists of a fully guarded lower framework, into which the electrical panel and control system are integrated. There is also an enclosed upper guard assembly with hinged and interlocked operator access doors.
The insertion machine is dual-sided, with each side featuring stepper motor-driven dual-function tractor drives:
- Side driving of the polyamide strip and correct seating of the glue wire.
- Glue wire de-reeling and feeding.
A third stepper motor controls a fixed overhead drive mechanism for transferring the polyamide strip, allowing for simultaneous glue wire insertion into the grooves on either side of the strip.
Glue wire de-reeling is achieved by looping the wire around a series of pulleys and then through the wire feed tractor drive, which is mechanically coupled/slaved from the main polyamide strip side drive. This side drive both transfers the strip and ensures the glue wire is correctly seated into the groove. Correct alignment of the glue wire with the grooves is achieved via an extended nozzle integrated into a cropping mechanism.
The machine design uses a series of sensors that interlock operations, ensuring that if the required conditions are not met, the machine will not operate. When the polyamide strip is manually inserted into the machine, its presence is confirmed. Together with the glue wire confirmation at both nozzles, this triggers the machine cycle, simultaneously advancing both the polyamide strip and glue wires. The operation continues until the end of the strip is detected, which triggers a pause in the strip transfer and activates the cropping units.
After cropping, the polyamide strip transfer resumes, drawing in and inserting the remainder of the cut glue wire. As the strip advances and exits the machine, the glue wire also advances through the cropping unit and nozzle, ensuring correct positioning for the next cycle. This sequencing compensates for any potential length variations.
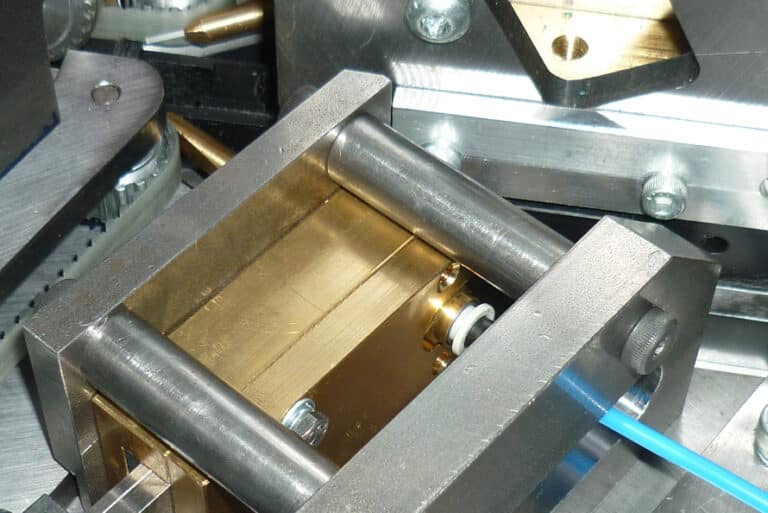

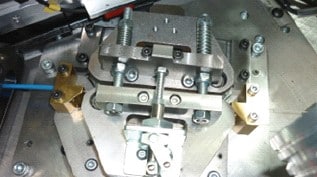
Synergy, since its formation in 2009, has built upon decades of experience to support UK manufacturing through its tailored services and the provision of automation and manufacturing solutions of various scales. We provide everything from Low-Cost Automation (LCA) to fully automated turnkey production facilities.
Synergy leverages its cross-industry expertise to deliver bespoke solutions, focusing on simplification and reducing complexity. We implement the latest technologies only when appropriate, favoring simpler, more cost-effective solutions where possible. This is achieved by gaining a deep understanding of our clients’ technical skill sets, operating procedures, and broader business needs, not just their immediate requirements.
This approach fosters long-term relationships, allowing us to provide continued support across multiple areas of our clients’ businesses, including sales and business development. Whether through Low-Cost Automation or fully automated systems, we help clients achieve increased productivity, improved quality, labor savings, enhanced safety, and cost-efficient manufacturing.
To discuss your requirements and find out how Synergy can support your manufacturing needs, get in touch with us today.