Automotive Trim Assembly
Overview
The client had initially intended that the insertion of steel cord rubber seals into the pre-formed and polished aluminium trims would be carried out manually. However, it quickly became apparent during the early stages of part supply that this approach was time-consuming and resulted in poor component quality. The solution was the semi-automated Seal Insertion Rig.
This is an example of Low-Cost Automation (LCA) supplied by Synergy to a long-term Tier 1 automotive parts manufacturer specializing in aluminium product manufacturing, from raw materials to value-added finished parts.
The Challenge
As with most automotive projects, there are a number of component variants: Front, Rear, Left Hand, and Right Hand. In addition, there was a further future-proofing requirement to accommodate other, similar, undefined components at a later date.
Solution
After being awarded the equipment contract, Synergy produced prototype tools to evaluate alternative concepts. This allowed for the assessment of assembly quality, both in terms of dimensional accuracy and surface finish and helped determine the optimal orientation of the components and the seal insertion mechanism.
The prototyping phase also confirmed that to achieve the required insertion quality, the insertion mechanism (roller) needed to mimic the 3D geometry (bend and twist) of the component. Utilizing 3D modelling techniques, combined with Synergy’s extensive experience, resulted in a pneumatically assisted, semi-automated rig with PLC control.
The solution featured a modular aluminium base frame with integrated storage shelves, sufficient to house current project tooling and anticipated future needs. The use of interchangeable tooling nests for multiple components was enabled by component-specific designs. The nests were designed for ease of handling (considering weight and size), with tapered dowels for easy single-person tool changes.
The insertion mechanism, pneumatically assisted with the X, Y, and Z axes, was combined with component-specific cam profiles integrated into each tool nest. Proximity sensors within the insertion mechanism, along with the PLC control system, ensured POKA-YOKE (fool-proofing), preventing incorrect usage of the mechanism.
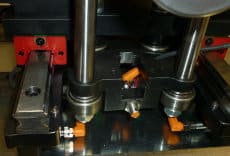
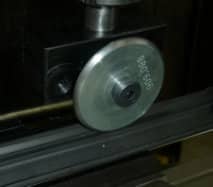
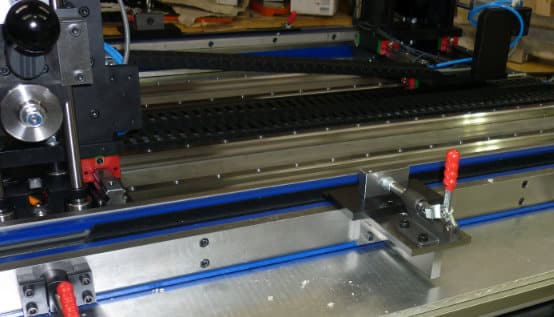
Synergy, since its formation in 2009, has built upon decades of experience to support UK manufacturing through its tailored services and the provision of automation and manufacturing solutions of various scales. We provide everything from Low-Cost Automation (LCA) to fully automated turnkey production facilities.
Synergy leverages its cross-industry expertise to deliver bespoke solutions, focusing on simplification and reducing complexity. We implement the latest technologies only when appropriate, favoring simpler, more cost-effective solutions where possible. This is achieved by gaining a deep understanding of our clients’ technical skill sets, operating procedures, and broader business needs, not just their immediate requirements.
This approach fosters long-term relationships, allowing us to provide continued support across multiple areas of our clients’ businesses, including sales and business development. Whether through Low-Cost Automation or fully automated systems, we help clients achieve increased productivity, improved quality, labor savings, enhanced safety, and cost-efficient manufacturing.
To discuss your requirements and find out how Synergy can support your manufacturing needs, get in touch with us today.