Window Bracket Manufacturing Cell
Overview & Challenge
During the initial concept and quotation phase, an analysis of the processing stages and material movements identified a bottleneck in the process. It was determined that 4 seconds would be insufficient for the pressing operation to be completed. The solution was to simultaneously process multiple components in the same step, achieved by processing pairs of extrusions. The transfer time for a pair of extrusions would be the same as for a single extrusion, allowing more time for the pressing operation while maintaining a maximum cycle time of 8 seconds per pair of components.
Early stages of the quotation process and discussions with the client quickly revealed that their budget, based on a previous simpler and lower-volume project, would be insufficient to meet the requirements of this project.
The Solution
These budgetary issues initially posed a potential project block. However, Synergy’s revised concepts, including magazine loading and part storage, offered labor savings by reducing the need for constant operator tending, thus allowing for reduced labor costs. This provided an alternative economic and budgetary strategy.
The overall footprint of the finished solution exceeds 8000mm in length and consists of three modules: the Loading/Transfer Module, the Press Module, and the Saw Module. Constructing the system in three separate modules offered logistical advantages for delivery and installation. Additionally, segregating the processes allowed for process isolation, which improved component quality by ensuring that the extrusion being processed was not influenced by other operations.
The integration of an interlocked airlock into the loading/transfer module improved operator productivity by allowing the magazine to be safely loaded at any time without stopping or pausing other machine operations. Operator safety is paramount, and the inner airlock prevents access to any moving parts inside the main machine guard. A two-handed control with a dead man’s switch is used to pivot the magazine storage mechanism out of the machine, facilitating operator access and ergonomics for component loading.
Component quality and tolerance are enhanced by using the pierced feature created in the first press operation as a reference for all downstream operations. This is achieved by means of expanding location pins.

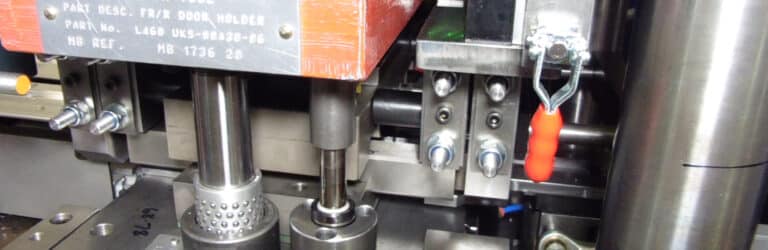
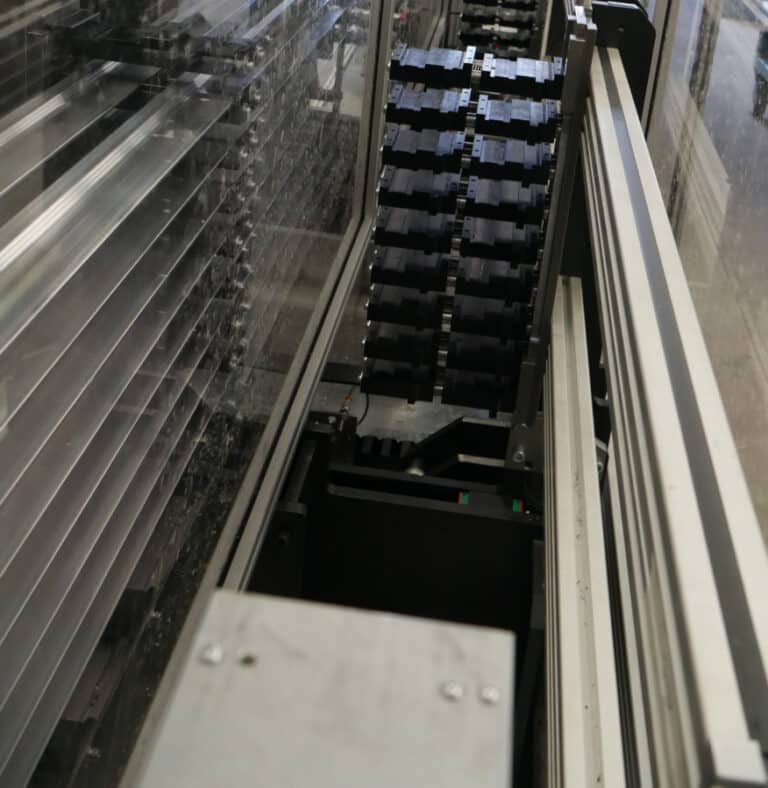
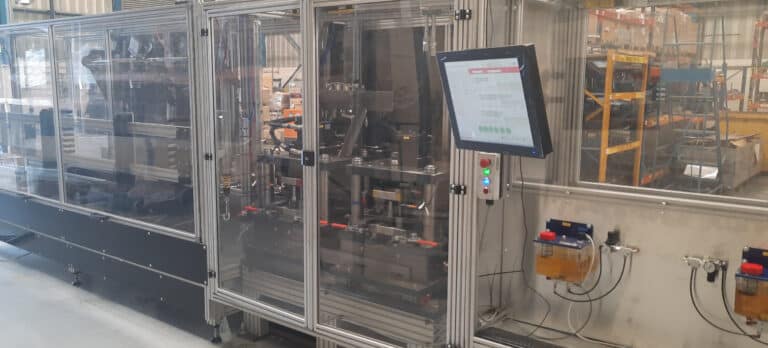
Synergy, since its formation in 2009, has built upon decades of experience to support UK manufacturing through its tailored services and the provision of automation and manufacturing solutions of various scales. We provide everything from Low-Cost Automation (LCA) to fully automated turnkey production facilities.
Synergy leverages its cross-industry expertise to deliver bespoke solutions, focusing on simplification and reducing complexity. We implement the latest technologies only when appropriate, favoring simpler, more cost-effective solutions where possible. This is achieved by gaining a deep understanding of our clients’ technical skill sets, operating procedures, and broader business needs, not just their immediate requirements.
This approach fosters long-term relationships, allowing us to provide continued support across multiple areas of our clients’ businesses, including sales and business development. Whether through Low-Cost Automation or fully automated systems, we help clients achieve increased productivity, improved quality, labor savings, enhanced safety, and cost-efficient manufacturing.
To discuss your requirements and find out how Synergy can support your manufacturing needs, get in touch with us today.