Hydraulic Pierce Rig
Overview
The Cantrail Pierce Rig is an example of the collaborative client-supplier approach used by Synergy. Synergy had been working on a project for a Tier 1 supplier to Bentley, providing stretch form equipment to produce Cantrail and Seal Carriers when an additional process requirement arose: to pierce mounting holes in the welded Cantrail and Seal Carrier assemblies. As is often the case, particularly within the automotive sector, achieving a cost-effective solution was essential.
The Challenge
The requirement:
- Pierce mounting holes in four variants of cantrail assemblies: Front, Rear, Left Hand, and Right Hand.
- Ensure ease of use by unskilled operators with minimal training.
- Any required tool changes should be carried out by the operator/setter without the need for engineering involvement.
- Tool changes should be minimised and take no longer than 15-20 minutes.
The Solution
By understanding the client’s operating processes, it became apparent that, due to upstream processes, components would be produced in variant-type batches. This realisation meant that instead of providing a machine similar to their existing one—which consisted of four component-specific stations set up to produce any of the four variants—we were able to provide a more cost-effective and energy-efficient solution using a simple type-change facility.
This approach allowed us to reduce the number of hydraulic actuators from 22 to just six, resulting in a much smaller hydraulic system. The pierce rig design incorporated four component-specific tooling plates, rotated into position via a counterbalanced pivot and manual hand wheel. Each tooling plate included pierce unit subplates, dowelled into position with integrated adjustment and jacking bolts on all four sides, offering future-proofing in case of component design changes.
Tool changes involved the removal and repositioning of the pierce units, which was achieved with a single screw (loosened but not removed). The pierce units were located via a hardened V and dowel mechanism, ensuring accuracy and repeatable positioning in all directions. The modular design of the pierce units minimised the mass to be lifted during type changes. The entire tool change process could be completed within 15 minutes.
Safe operation was ensured through the use of perimeter guarding and pressure mats. Additionally, the design of the pierce tools prevented material ejection.
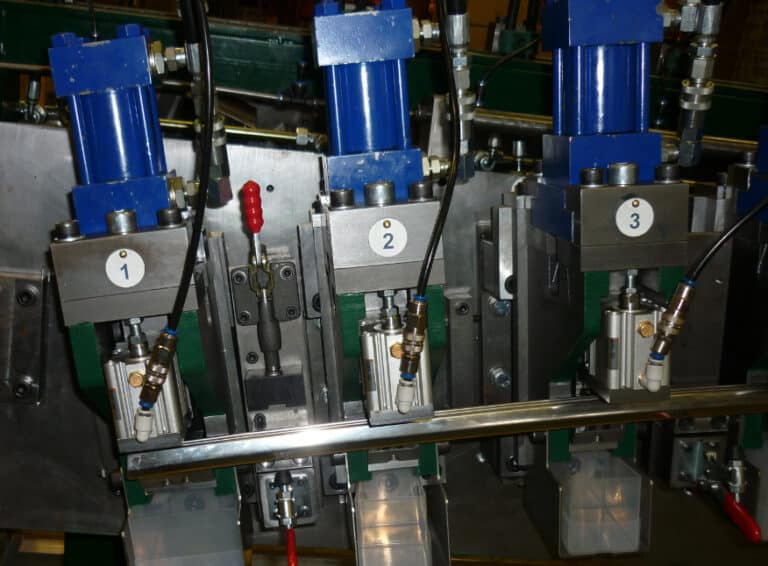
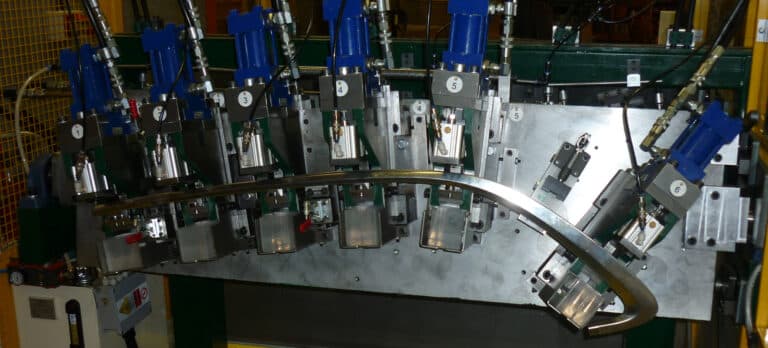
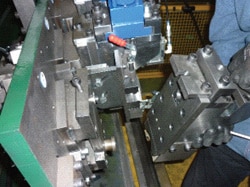
Synergy, since its formation in 2009, has built upon decades of experience to support UK manufacturing through its tailored services and the provision of automation and manufacturing solutions of various scales. We provide everything from Low-Cost Automation (LCA) to fully automated turnkey production facilities.
Synergy leverages its cross-industry expertise to deliver bespoke solutions, focusing on simplification and reducing complexity. We implement the latest technologies only when appropriate, favoring simpler, more cost-effective solutions where possible. This is achieved by gaining a deep understanding of our clients’ technical skill sets, operating procedures, and broader business needs, not just their immediate requirements.
This approach fosters long-term relationships, allowing us to provide continued support across multiple areas of our clients’ businesses, including sales and business development. Whether through Low-Cost Automation or fully automated systems, we help clients achieve increased productivity, improved quality, labor savings, enhanced safety, and cost-efficient manufacturing.
To discuss your requirements and find out how Synergy can support your manufacturing needs, get in touch with us today.