Multi-Headed Saw
Overview & Challenge
The requirement was to allow end trimming pairs of Stretch formed components for the Ford S- Max project. The 1st challenge was to accommodate the trimming of 2 different variants with different section, geometry, and compound angle cut conditions. The 2nd challenge was due to the component material, which was a special grade of stainless steel, which imposed specific cutting speed and feed constraints.
The Solution
The component variations were accommodated through the use of component specific type change tooling nests, with integrated presence sensing.
Multi axis mounting brackets, allowed each saw head to be indexed/locked into predefined positions, thus achieving the correct component specific compound angle cuts.
The use of proximity sensing integrated into the saw assemblies, and component nest confirms both the presence of / and type of tooling nest, correct saw index position and component presence. This ensures that machine operation is only permitted if all required conditions are achieved.
This Poka-Yoke, through the use of sensors, simplified operator interaction, improving productivity and machine utilisation by eliminating the risk of damage to the machine/tooling which would result from incorrect setup.
Operator safety was maintained through the use of fully enclosed and interlocked guarding. Hinged poly-carbonate doors on 3 sides allowed easy access for type change or TPM activities. Normal operator access is provided via an interlocked, counter balanced vertical rising door. The rising door lock mechanism is automatically latched during machine operation, and is only released once the saw blades have stopped rotating, allowing the door to open in a controlled manner, under the action of the counter balance. This results in improved operator interaction, and productivity. Interaction with the door is limited to manually lowering, after component loading and removal has been completed.
Operator interaction is further improved through the use of an integrated unloading mechanism. The sawn components are automatically removed, from the tooling nest, and while the saw rotation comes to a stop, are transferred to a park position, awaiting manual removal. This ensures that the load area is clear to receive the next component pair.
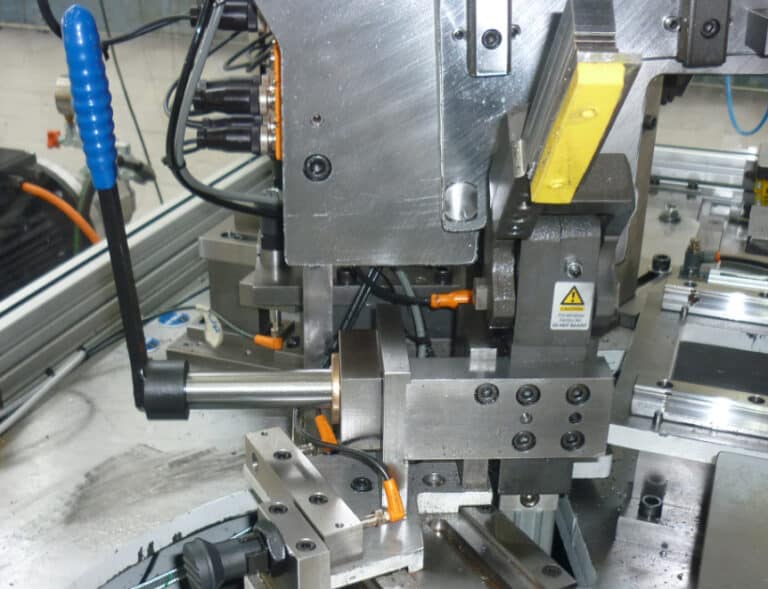
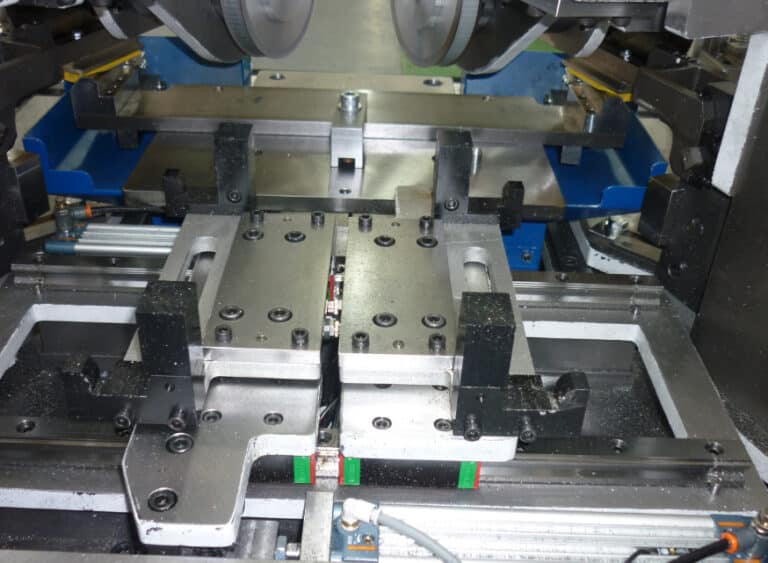
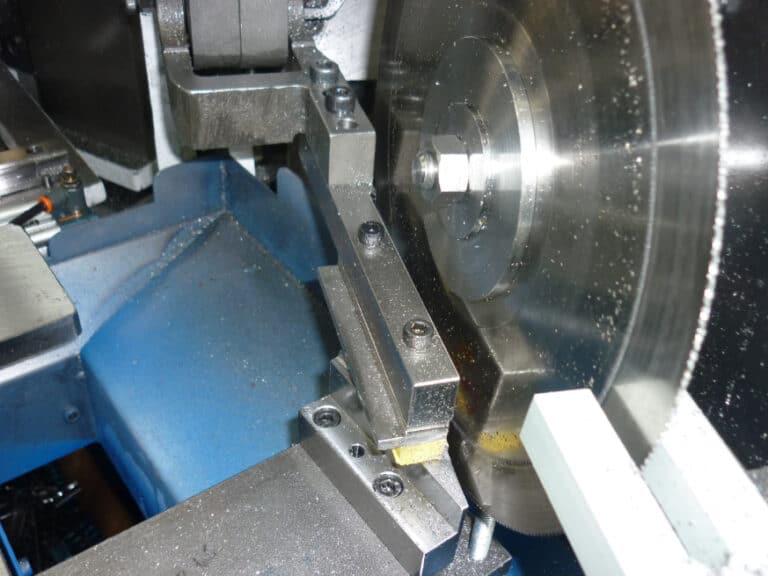
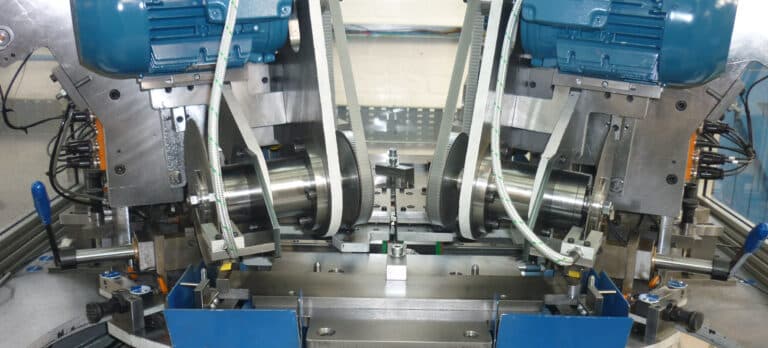
Synergy, since its formation in 2009, has built upon decades of experience to support UK manufacturing through its tailored services and the provision of automation and manufacturing solutions of various scales. We provide everything from Low-Cost Automation (LCA) to fully automated turnkey production facilities.
Synergy leverages its cross-industry expertise to deliver bespoke solutions, focusing on simplification and reducing complexity. We implement the latest technologies only when appropriate, favoring simpler, more cost-effective solutions where possible. This is achieved by gaining a deep understanding of our clients’ technical skill sets, operating procedures, and broader business needs, not just their immediate requirements.
This approach fosters long-term relationships, allowing us to provide continued support across multiple areas of our clients’ businesses, including sales and business development. Whether through Low-Cost Automation or fully automated systems, we help clients achieve increased productivity, improved quality, labor savings, enhanced safety, and cost-efficient manufacturing.
To discuss your requirements and find out how Synergy can support your manufacturing needs, get in touch with us today.